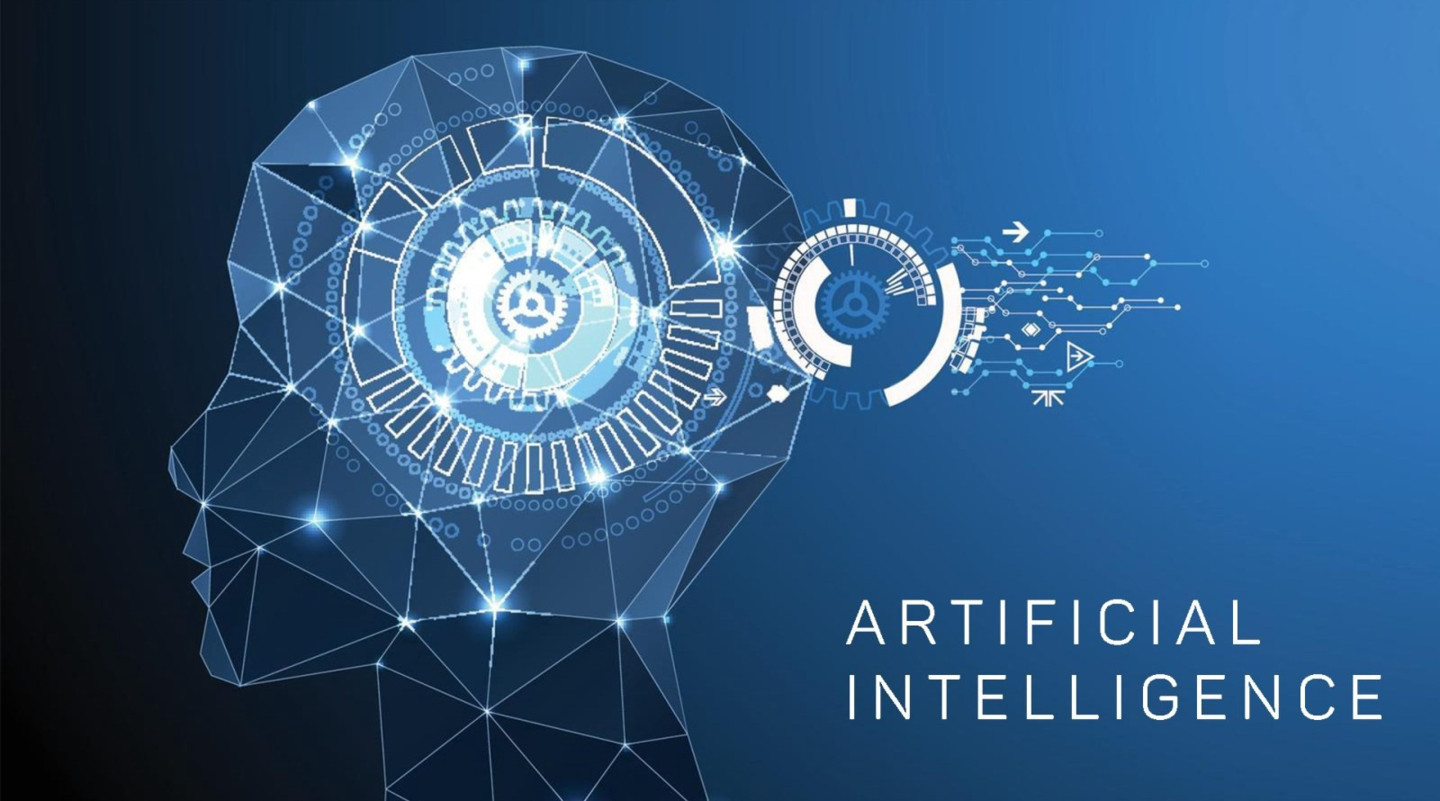
TFL is using AI to manage Safety Data Sheets
The leather chemicals group decided to use a digital tool to support customers worldwide
Keep reading...Browsing the magazine online is free upon registration.
Browse the libraryThe leather chemicals group decided to use a digital tool to support customers worldwide
Keep reading...Discover the trend colours proposed by the Italian leather chemicals group
Keep reading...
AICC's weight in the international representative body grows
Important environmental, social and governance goals already achieved
Keep reading...Inspirations and new leather colours for clothing, footwear, accessories and upholstery
Keep reading...In the beautiful Castelfranco headquarters, the management team of the Tuscan leather chemicals company illustrates the new company course, which aims to offer customers a complete assistance service from the wet phase to the finishing phase rifinizione
Keep reading...The Tuscan mechanical engineering company specialising in the design of leather handling, drying and conditioning systems is booming
Keep reading...New work by the Leather Station highlights the positive environmental balance of leather processing
Keep reading...Joan Carles Castell, the new IULTCS president, is optimistic about the future of the leather industry, thanks to scientific and technological advances that will enable it to overcome environmental challenges
Keep reading...Silvateam S.p.A. and wet-green GmbH are joining forces. They represent the benchmark in bio-circular and bio-based tanning technologies.
Keep reading...The Veneto-based leather chemicals company has obtained ZDHC Level 3 compliance
Keep reading...In the document, the Tuscan tannery reports on its current commitment and future objectives
Keep reading...This content requires a subscription to view. Are you already a subscriber? Sign in